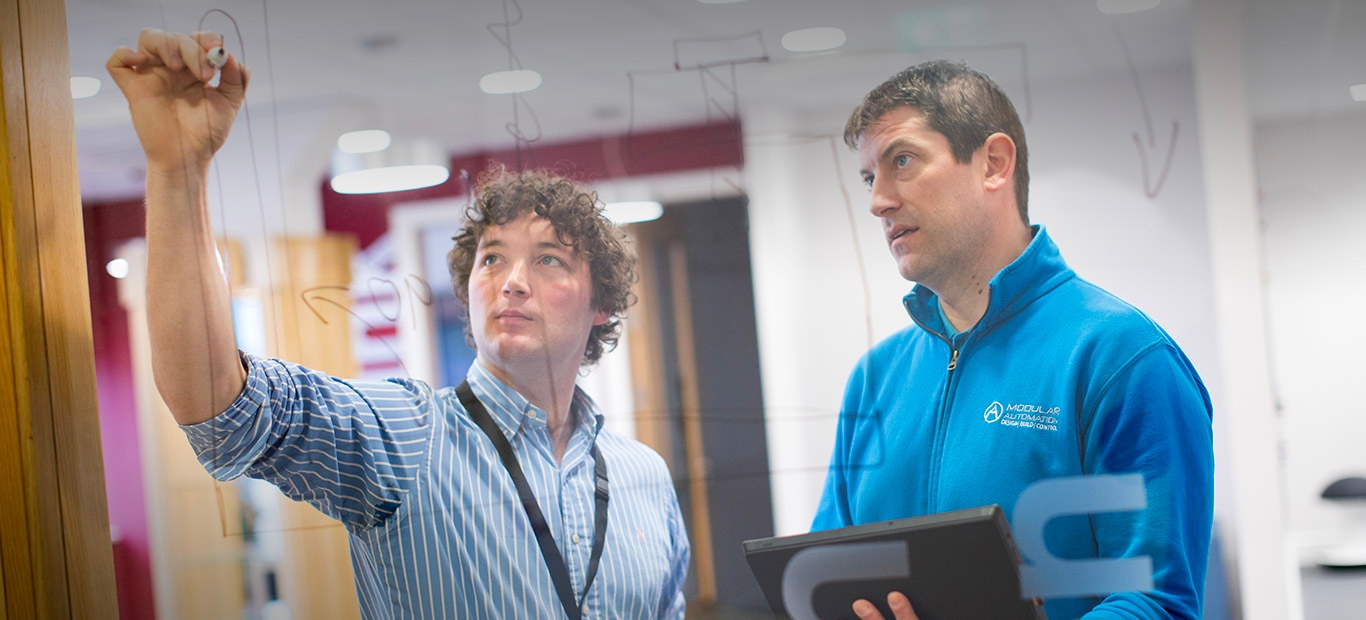
Automation Exploration
Steering the right automation journey
The right automation, in the right place, at the right time.
We operate as a close, trusted, automation partner to the world’s leading MedTech manufacturers, helping them to explore their automation opportunities, large and small. Collaborating closely with our customers, going deep to fully understand what they want to achieve, with a focus on delivering the best ROI possible. Our role is to guide and steer, using our 35 years of automation expertise to scope and plan a solution that delivers on the requirements, every time.
How we do it.
-
Understand the needs
We collaborate closely with our customers to understand their needs, with particular focus on the ROI they’re hoping to achieve, from reducing overheads and improving safety, to increasing capacity or throughput. -
Learn the processes
We learn and assess the processes our customer uses in manufacturing, including the materials, the products and the applications. -
Concept Development
A learning phase for both our customer and Modular, we develop a concept for the automation project, featuring the equipment or manufacturing line, helping to visualise the final implementation. The methodology helps to identifies the risks and feasibility of the project, providing greater clarity in terms of project execution, the equipment that will be used, how long it will take and what the overall budget will be. -
Proof-of-Principle
Our Proof-of-Principle (PoP) methodology is used to de-risk the processes identified at the Concept Development stage, prior to commencing the main project. This clarifies the approach, timeline and budget. It’s the final step to ensure the automation project will meet the needs of the customer exactly as intended. -
Final proposal
Once the Concept Development and PoP are complete, our team set out the final proposal for the delivery of the custom automation solution.
Proof of Principle (PoP)
Assess feasibility. De-risk processes. Enter full-scale development with confidence.
Our PoP methodology is a quick, cost-effective process used to eliminate project risks at the concept stage. Through rapid prototyping and reduced-scale trials, risks are isolated and mitigated as we test, validate and then refine. The results help to deliver more accurate cost and development forecasts for the project, ensuring our customers enter full-scale development with confidence that the solution will deliver as intended.
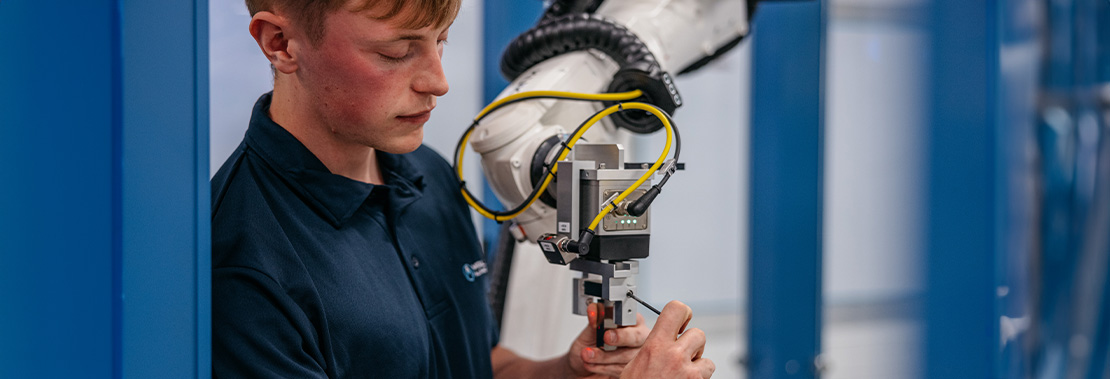
Why Modular for Automation Exploration?
The longevity and experience to deliver innovative, challenging solutions.
For over 35 years our expert engineers have planned, designed and built the most innovative, complex, challenging automation equipment solutions for MedTech manufacturers. We’ve never failed a customer. We always, always deliver.
Technology pioneers driving the most complex of integrations.
We’re an engineering technology company developing smart machines using the latest technologies. We take risks, we test, trial and explore new technologies, new innovations, new integrations. Always ready to use the latest, most advanced technologies to power innovation. Allowing us to take on the most complex, challenging projects and providing our customers with a competitive edge.
Deep collaboration is in our nature.
A multi-disciplined team with the capability, knowledge, passion, ingenuity, and confidence to work shoulder-to-shoulder with the world’s most advanced MedTech manufacturers. We go deep to truly understand their needs, their processes, their materials, products and applications. Arming ourselves with the intel to deliver the right solution, every time.
De-risk with PoP. Enter full-scale development with confidence.
Our Proof of Principle (PoP) methodology is a quick, cost-effective process used to eliminate project risks at the concept stage. Allowing for more accurate cost and development forecasts, this proven approach ensures our customers enter full-scale development with confidence that the project will deliver as intended.
Extensive knowledge of regulations, standards, and protocols.
Experience of automation protocols for regulated environments including equipment installed into clean rooms (ISO class 7 & 8), ATEX & high temperature environments 200°C+ and sealed nitrogen environments. Computer system validation (CSV) to GEP/GMP regulations and qualification to GAMP requirements and our Software Development Life Cycle model (V-model).
Case Study
The Proof of Principle (PoP)
Modular are at their best when developing complex custom solutions to advanced manufacturing challenges—a process that takes substantial talent, precision skills and a healthy appetite for…
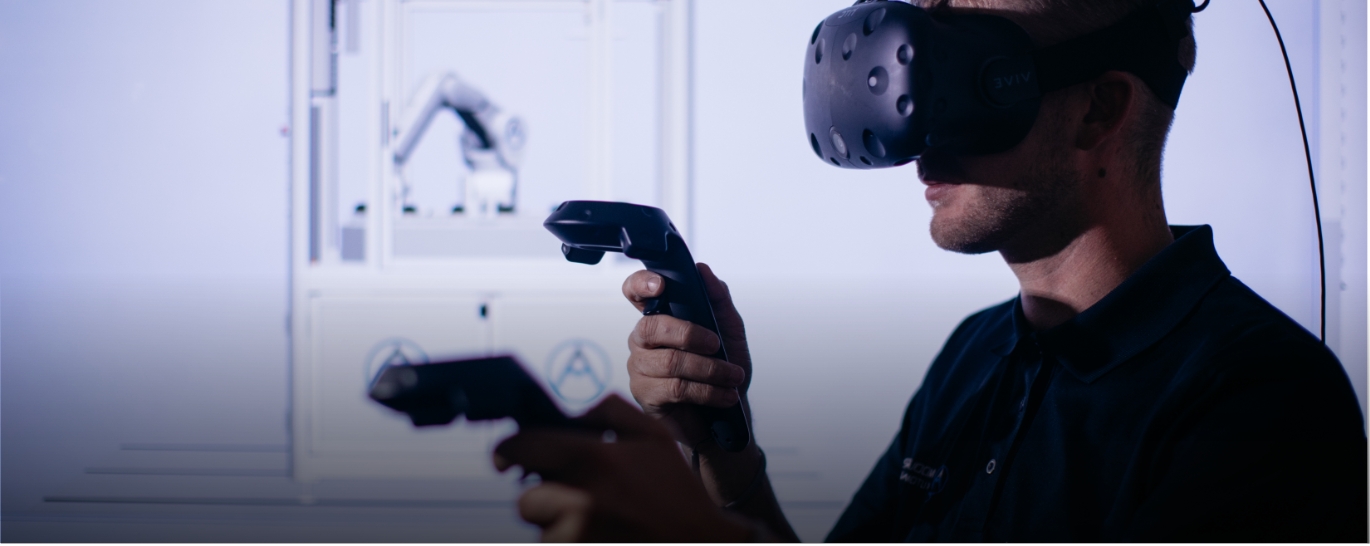
Let’s Talk
Tell us about your manufacturing challenge, and one of our senior engineers will be in touch to explore how we can help.
Contact Us